Ce post n’est pas un tutoriel pour la configuration du Skeinforge, c’est plutôt un carnet de bord sur mon avancée pour sa compréhension. J’espère ainsi pouvoir en éditer un véritable article, plus compact et pratique…
Logiciel/matériel utilisé
ReplicatorG 037 avec Skeinforge 050.
Thing-O-Matic avec extrudeur MK 7 et plastique ABS blanc 1.75. Nez avec un diamètre de 0.4.
Skeinforge?
Skeinforge est un générateur de GCode utilisé par ReplicatorG via, dans les plus récentes versions, le module Print-O-Matic. Ce dernier est l’interface qui s’ouvre lorqu’à partir de ReplicatorG, vous voulez générer un GCode (bouton en bas à droite).
Ouvrir le tableau de paramètre depuis ReplicatorG:
Edit -> Edit Profile puis Edit
Lorsqu’on veut éditer le tableau de paramètre proposé par Skeinforge, on se retrouve avec une énorme quantité de paramètres à régler. Certains d’entre eux sont plus importants que d’autres.
Une documentation/tuto est disponible ici (en anglais).
Les termes communs du Skeinforge
Extrait du Blog de Dave Durant.
Flow rate (RPM): en combien de temps l’extruder va ‘tirer’ une certaine distance de fil. Vitesse d’extrusion ou d’écoulement. RPM = Revolution Per Minute = Nbe de tour / Minute
Feed rate (mm/s): Vitesse de déplacement de la plateforme horizontale ou de l’extrusion en x et y.
Thickness/height: hauteur d’une couche de plastique.
Width: Largeur du plastique déposé ou du nez d’impression (nozzle)
Perimeter/edge: la couche externe/bordure de l’objet à imprimer.
Infill: Ce qui va être imprimé à l’intérieur des lignes de périmètre.
Shells: couche supplémentaire de la couche externe. Il peut ainsi y avoir plusieurs couches pour former l’extérieur de la forme.
Over: veut dire « diviser par », c’est-à-dire, « A over B » -> « A/B ». Il y a plus de 190 paramètres « A over B » dans Skeinforge. Si on a « A over B = 2 », ça veut juste dire que la valeur de A est deux fois supérieure à la valeur de B; « A over B = 1 » veut dire que la valeur de A vaut celle de B.
Multiplier: similaire à « Over ». C’est une manière de décrire le ratio de la valeur concernée par rapport à la valeur en général. Par exemple: » Object First Layer Feed Rate Infill Multiplier (ratio) = 0.9″ dans « Speed » dit que l’impression de la première couche se fera à 90% de vitesse du « Feed Rate » générique.
Travel: Quand le nez d’impression se déplace (d’un spot à un autre par exemple) sans imprimer.
Raft: Première couche ajouté à l’objet (en général, plus large) comme support d’adhérence. Il est composé d’une « base layer » et d’une « interface layer ».
Object First Layer: première couche de l’objet. Celle-ci sera soit sur un raft, soit directement sur la plateforme. Dans les deux cas, la paramètrisation de la vitesse de déplacement du nez est importante.
Bridge: Quand on imprime sur du vide. Normalement, l’impression se fait couche sur couche, mais il peut être possible d’imprimer un ‘pont’ entre deux parties d’un objet.
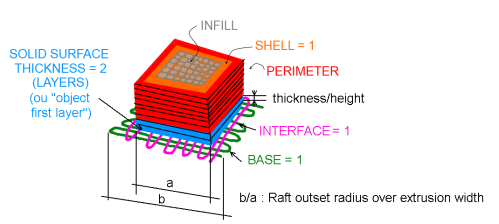
Les paramètres « inutiles »
Selon le site de Makerbot, les paramètres de
- Comb
- Cool
- Hop
- Multiply
- Oozebane
- Stretch
- Unpause
- Wipe
- Polyfile (disparu sur la version 0050)
sont « inutiles » dans un premier temps. Ils conseillent de désactiver ces dernier. Ils seront discutés dans un prochain post.
Paramètres importants
Dimension
Remplir la valeur de Filament Diameter (-> 1.75 mm dans mon cas) et de Filament Packing Density (-> 0.85-0.9 pour du ABS)
Fill
Ces paramètres déterminent comment le Makerbot va « remplir » l’objet à imprimer. Ce remplissage servira notamment comme support aux dernières couches.
Solid Surface Thickness (Layers)
Malgrès le nom de ce paramètre, celui-ci est le nombre de couche remplie avant et après avoir entamé le remplissage intérieur (et non pas leur hauteur). L’imprimante va d’abord (et à la fin) imprimer X couche pleine avant d’imprimer les couches avec le ratio défini dans le Print-O-Matic (la fenêtre qui s’ouvre lorsqu’on veut générer le GCode -> bouton en bas à droite du ReplicatorG). On conseille de mettre 3.
Extra Shells…
Pour les 3 prochains paramètres, la valeur 1 semble donner de bons résultats. Plus il y a de « Shell », plus solide sera l’objet.
« … On Sparse Layers »
C’est le paramètre qui détermine combien de couches forment les parois extérieures (qui ne sont pas sur les premières/dernières couches, i.e. ce sont les couches de « infill ») de l’objet.
« … On Base Layers »
Ce sont le nombre de couche de parois extérieur sur toutes les couches remplies (dont la première) d’ordre impaire.
« … On Alternating Solid Layers »
Ce sont le nombre de couches de parois extérieures sur toutes les couches remplies (dont la dernière) d’ordre paire.
Infill Pattern
-> « Grid Rectangular ». L’option « Line » prendra moins de temps, l’option « Grid Hexagonal » beaucoup plus, et « Grid Rectangular » sera entre les deux.
Infill Solidity
Le % de plastique qui sera déposé à l’intérieur de l’objet (ex: 0.4 = 40% de plastique)
Raft (ou radeau)
Le raft sert comme base à un objet: ainsi, on est sûr que l’objet adhère à la plateforme, et en plus, il nous aide à enlever l’objet une fois celui ci imprimé.
Le raft est composé de deux couches: la base et l’interface.
Il se trouve que l’interface est difficile à enlever et qu’il est conseillé de ne pas imprimer cette dernière (c’est -à-dire d’imprimer que la base du raft). Ainsi, il faut mettre la valeur 0 à « Interface Layer ».
Apparemment, les meilleurs radeaux sont ceux qui ne sont pas trop hauts, et avec de petits intervalles. Il faut utiliser un outil coupant type ciseau à bois pour les faires sauter un par un de l’objet.
En général, avec une plateforme chauffante automatique (Automated Heated Platform), il n’est pas nécessaire de créer un raft. Dans ce cas là, on dit qu’on imprime « raftless » et il faut alors tout miser sur les premières couches pour que l’adhérence se fasse correctement.
On peut jouer sur plusieurs paramètres pour améliorer l’adhérence du raft sur la plateforme:
- Augmenter la T° du bed.
- Augmenter de quelques décimales le « Base Layer Thickness over Layer Thickness«
Si trop de plastique est déposé, on peut diminuer la valeur de « Base Infill Density » et vice-versa. Comme on peut aussi changer les paramètres de « layer height », « feedrate », etc. ce dernier paramètre pourra être souvent calibré.
« Raft Outset Radius Over Extrusion Width » (n’est pas dans Skeinforge 50): largeur du raft par rapport au diamètre de l’objet. Un grand raft donne moins de déformation. Sa valeur doit rester autour de 15, sauf pour les grands objets (où le raft doit rester sur la plateforme).
Pour aller plus loin… (en anglais)
Imprimer sans raft
Il est conseillé de garder l’option « Raft » mais de paramétrer le nombre de « base layer » et d' »interface layer » à 0. De plus il faut jouer avec le flowrate/feedrate de la première couche.
Configuration fondamentale
« Layer Height« , « Flowrate » et « Feedrate » contrôlent l’aspect physique de l’objet. « Extrusion Rate » va contrôler plutôt les distances entre les lignes d’impression. Dans un prochain post, je parlerai plus en détail de leur rapport et d’une calibration.
Layer Height
Dans l’option « Carve » (sculpter, tailler). Contrôle l’épaisseur de chaques couche. Recommandé: 0.3-0.35mm (compte tenu de la buse de 0.4 mm)
Flowrate
Dans l’option « Speed ». C’est la vitesse d’extrusion (sortie du plastique). Il est conseillé de régler ce paramètre au maximum (255) pour éviter des irrégularité dans le plastique déposé.
ATTENTION: Il semblerait que le flowrate indiqué à un facteur de 10, c’est-à-dire que pour avoir 12 RPM, il faut configurer la valeur à 120. Alternative: Si il est indiqué « Flowrate (Float) », les valeurs à mettre ne doivent pas être multipliées par 10 (?)
Feedrate
Dans l’option « Speed ». C’est la vitesse de déplacement de la plateforme (i.e. mouvement horizontal x et y). Un bon réglage est 35mm/s.
…Over Flowrate & …Over Feedrate
Plusieurs options prennent en compte le rapport de vitesse que l’impression aura lorsque certaines parties seront imprimées. Les parties en question sont (dans l’onglet « Speed »):
- Edge/perimeter
- First object layer
Pour ces parties-là, il vaut mieux régler une vitesse plus lente que pour le reste. En effet, par rapport à la première couche, il est nécessaire que le plastique adhère à la surface de la plateforme. Pour les « edges », comme ils donnent la structure de l’objet, il est important qu’ils soient bien déposés. On peut mettre un ratio de 0.5.
Extrusion width
Séparé en trois paramètres, ce paramètre gère le placement des lignes d’impression:
- « Extrusion Width over Thickness » (option « Inset »): densité entre les lignes de remplissage. Plus la valeur est haute, plus les lignes seront éloignées les unes des autres: diminuer ce paramètre si le remplissage semple trop dense.
- « Extrusion Perimeter Width over Thickness » (option « Carve »): Idem mais pour le périmètre/edge.
- « Extrusion Diameter over Thickness » ??? Pas trouvé dans la version 50 de Skeinforge
Le 1. et le 2. doivent être paramétrés à la même valeur.
Altitude
Cet onglet propose de gérer un delta de hauteur Z pour l’impression de l’objet. Il est assez pratique de jouer avec cette valeur pour pouvoir gérer l’apparence de l’objet – notamment pour éviter un écrasement à sa base et donc une hauteur totale inférieure à celle désirée.
Aides au paramétrage
Plusieurs personnes ont proposées leur savoir-faire pour ne pas rendre la paramétrisation du Skeinforge trop laborieuse…
Le tableau Excel de Starno
Ici, vous trouverez un fichier de tableur (à télécharger et à ouvrir avec OpenOffice ou Excel). Plusieurs données sont requises:
- Propriétés de l’extrudeur;
- « Fudge Factor » ou facteur de truquages (pour les petites nuances dans l’impression);
- Input désirées (comme la vitesse de dépôt, etc.);
Une fois rentrée, ce tableau renvois les paramètres à remplir dans le Skeinforge.
La version (encore plus) simplifiée de MakerBlock
Dans ce site, on peut trouver beaucoup d’informations sur l’impression 3D, mais le plus remarquable reste le ProfileMaker qui permet en deux clics d’obtenir les paramètres les plus basiques pour le Skeinforge…
- Hauteur de couche de plastique déposé désiré
- Diamètre du fil
- Diamètre du nez
Dans mon cas, j’ai entré les paramètres suivants:

Paramètres calculés pour le Skeinforge
/!\ « Infill Width over Thickness ratio » -> se trouve dans « Inset »
J’ai imprimé un parallélépipède de L20 x l20 x h10, et ai obtenu une erreur de l’ordre du 0.5mm.